Long packs should be unloaded either with the use of spreader beam or long belts.
- Characteristics
- Instructions
- Applications
- Certificates

CODE / ΚΩΔ.: TR 75/200
Conditions for the calculation of permitible loads
In the case of a load bearing floor, the load to consider is the sum of the weight of the sheet, the other inert material and the ordinary working load on the floor.
The geometric and the static characteristics are calculated according to the Eurocode 3 for the profiles and the Eurocode 4 for the composite slabs.
The dimensional criteria of the trapezoidal section and the composite slab were based to the following standards:
EC3 EN 1993-1-1, EN 1993-1-3, EN 1993-1-5, EC4 EN 1994-1-1.
Regarding the material quality, the following bearing capacity categories were used about the trapezoidal metal sheet and the concrete:
Steel S320GD (ΕΝ 10346:2015), fy=320 MPa.
Concrete C25/30.
Support width at the edge 50mm and in the middle 75mm.
The loading limit values were tested in order to meet the functional demands, with maximum bending arrow L/250, under the condition of cracked slab, ignoring the creeping phenomenon.
The loads were calculated under the condition of the use of a grid diameter Ø8mm welded mesh 150, 2cm under the concrete surface, as a negative reinforcement to the supporting points and the installation of temporary support at the middle of each span until concrete gets solid.
Table of mechanical properties and permitible loads for metal sheet TR 75/200

tnom: Metal thickness, Ρ: Metal weight, J: Moment of inertia for the section, W: Section modulus for the section surface,
Α: SINGLE SPAN, Β: MULTIPLE SPAN.
Table of mechanical properties and permitible loads for composite slabs TR 75/200

H: Composite slab height, tnom: metal thickness, P: Composite slab weight, Juncracked: Moment of inertia in uncracked condition, Jcracked: Moment of inertia in cracked condition, Vrd: Shear strength, Mpl,rd+: Resistance to positive moments, Mpl,rd-: Resistance to negative moments,
Α: SINGLE SPAN, Β: MULTIPLE SPAN.
ΝΟΤΕ: The values of the tables should be used only during pre-study stage. For detailed calculations the engineer must carry out his own study.
Installation
The metal sheets are assembled by fixing a layer of sheets to the support beams. This layer will then accept the successive concrete casting. These sheets must be free of oil or other dirt so as not to degrade material collaboration. Fixing to the beams can be performed using self-threading screws, nails or by welded shear connections having in mind that the sheets are never overlaid but brought section to section. The longitudinal joints are fixed every 0,50-0,80m, by screws or rivets, to prevent displacement of edges during casting.
To avoid cracking and for better load distribution, we advise laying an electrically welded grid 2cm from the upper surface of the concrete. Casting is performed by firstly trying to deposit the concrete at the supports and then by distributing it in a gradual way. The use of struts to the middle of each bay is recommended until the concrete gets solid.
To avoid cracking and for better load distribution, we advise laying an electrically welded grid 2cm from the upper surface of the concrete. Casting is performed by firstly trying to deposit the concrete at the supports and then by distributing it in a gradual way. The use of struts to the middle of each bay is recommended until the concrete gets solid.
PROJECT 33
Galvanized
length (mm) | small | big | weight (kg/m) | weight (kg/m2) | quantity | price per unit (€) | value (€) | Comments |
You might also need these products
Composite slabs TR 75/200
The high bearing capacity corrugated metal sheets DOMOLAM, are produced in a wide range and are used in composite slabs and permanent metal reinforcements for industrial and residential constructions. The collaboration between the metal sheet and the casting (concrete) is achieved through embossments capable of anchoring the casting impeding its detachment. The worked sheet therefore acts both as formwork during casting and as reinforcement, allowing the composites labs to carry higher loads in comparison to the traditional floors. They are produced in thickness up to 2,00mm according to EN 1090-1:2009+A1:2011 and have CE marking.
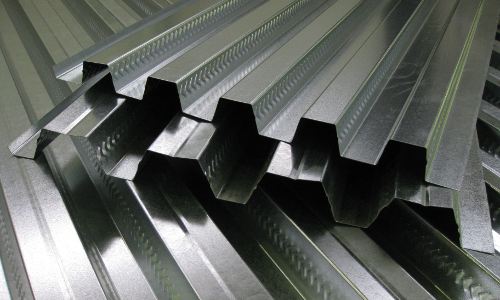
Composite slabs metal sheets points of excellence
1. Easy installation and modifications through cuts, additions, welding and nailing even on existing cunstructions.
2. Less weight construction for the same payload.
3. Shorter construction time overall, because of the possibility of simultaneous work on different floors.
4. Lower transportation cost in relation to other traditional precast elements.